Gravity Battery
Version 2
The second iteration solved an important problem—finding appropriate gears and having access to a CNC mill to machine the gearbox plates reduced the accessibility of the gravity battery to those with sophisticated machinery and a relatively high degree of mechanical knowledge. The solution was found through adapting a simple 125cc motorcycle engine donated by a local breaker.
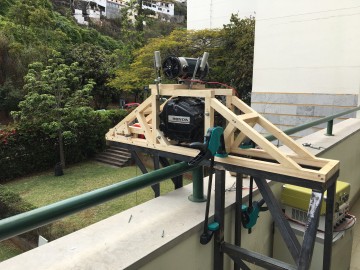
The main premise of this iteration was to reduce to complex making through using the high-quality gearboxes that exist in small motorcycles across the world. A brief explanation:
- Normally a motorcycle engine burns fossil fuel (petrol) to move the piston down. This is converted to rotary motion via the crankshaft (every 4th stroke in the case of the engine that was donated to us).
- Rotary motion (or RPM) is modified by the gearbox to ultimately rotate the rear wheel via a chain drive providing forward linear motion to the bike (and rider).
- The gravity battery reverses this situation: instead of fossil fuel, gravity spins the rear wheel using the hub as a pulley attached to a falling mass.
- This spins the drive sprocket, increasing RPM through the gearbox and finally driving the crankshaft at a speed determined by the selected gear, the diameter of the pulley, and the size of the falling mass.
- Motorcycles typically generate electrical power (for the starter motor, lights, etc.) using a generator spinning on the end of the crankshaft. Unfortunately, in our case, the breaker had already sold on this key component before we received the donated bike. For this test we used the same DC motor as the first prototype, connected to the crankshaft via the timing chain and modified gears.
- Unfortunately the frame was also missing so we had to construct a basic wooden structure to connect the pulley to the gearbox. In future versions we used the motorcycle frame and rear wheel reducing the complex making even further.
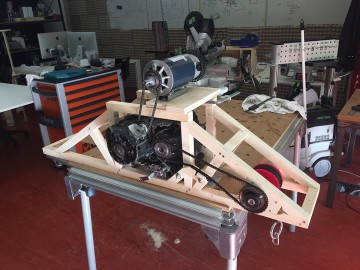
This worked relatively well but after analysing the system we observed that the starter motor gears spun much faster than the crank. Using these we increased substantially the ratio between the rotational speed of the rear wheel and the speed of the generator (approximately 1:120), in turn demanding an increase in the size of the falling mass (to overcome the increased torque) and more importantly the amount of energy the system was capable of generating / storing.